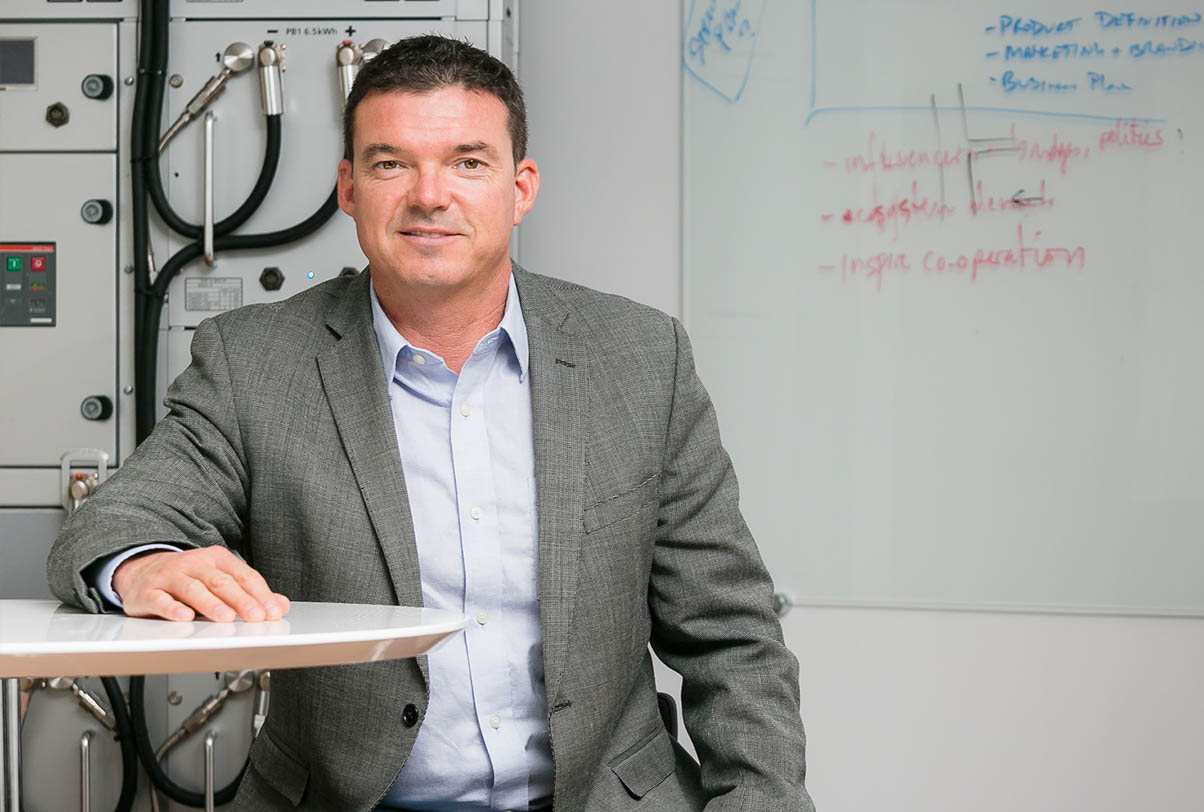
DNV-GL recently found that more fully-electric or hybrid-electric vessels were under in operation or under construction than there are LNG vessels, while projects like the installation of a 600kWh battery on the Maersk Cape Town and the construction of the zero emission hybrid container ship the Yara Birkeland provide proof that energy storage is viable on larger vessels.
One of the main misconceptions around electrified shipping is the understanding of the roles that Energy Storage Systems (ESS) can play on board a vessel. Using an ESS means different things in different vessels today.
Short range or smaller vessels are able to take advantage of huge fuel cost savings from fully-electric propulsion, while passenger vessels are also able to take full advantage of the operational benefits of the systems – with fewer vibrations, less noise and no emissions on deck improving passenger experiences. Hybrid propulsion is proving its value for more versatile or mid-range vessels, while battery solutions are gaining traction in the containership and tanker markets for auxiliary power supplies.
This is set to become an even more important factor for shipowners over the coming years.
Regulators are setting their sights on decarbonisation, both internationally and regionally, and new several new ‘zero-carbon’ fuels are in the latter stages of development. All of these fuels can benefit from energy storage for efficiency and viability; we believe that in the near future, all commercial ships will have a battery room to supplement other energy solutions.
Expansion of energy storage supply is therefore expected to accelerate in the next few years. As this happens, the industry must be cautious to ensure that safety is not side-lined in a rush to provide systems quickly – or that look to be cheaper on paper. To facilitate this, suppliers must take an honest and safety-focussed approach.
Modern ESS utilise lithium-ion cells as the energy source inside the battery. The most prominent risk with these cells is thermal runaway.
Thermal runaway starts when a single lithium-ion cell is damaged. This damaged cell then heats up, releasing toxic, flammable gasses. Unmitigated, the heat from one failed cell will damage surrounding cells. To deliver a valuable amount of energy, a maritime battery requires many banks of cells – meaning that a damaged cell can quickly turn into a potentially catastrophic chain reaction.
Excess loads placed on the battery such as those from over or under charging, as well as physical damage and general wear and tear, increase the risk of cell failure. However, even when a battery operates at optimum levels non-stop throughout its lifecycle, there is always a small risk that a cell is delivered with an undetectable fault.
Many manufacturers have not yet been clear about the significance of these risks, or how they can by managed. Holistic ESS design, starting with the cooling system and the space around the battery, can bring these risks to near zero, while delivering a less expensive system.
Ensuring safe systems
The space surrounding a marine battery must form part of the system’s design to ensure safety and efficiency. Safety systems must be integrated from the start of this design process to make sure that they work as efficiently as possible and ensure that these systems work together in harmony. They are not optional add-ons, but vital parts of any system that should not be sold separately.
The first stage of this design must look at cell cooling. Cell cooling can cut the risk of thermal runaway, or slow or stop a chain reaction when a damaged cell starts to heat. Integrated liquid cooling can stop thermal runaway – and deliver better battery performance.
A truly effective cooling system must cool the whole of the cells uniformly. When designed as part of the system from inception, water cooling can deliver uniform temperature control and remove “hot spots” on the cells. These hot spots will degrade the cells, and over time will cause premature failure.
Liquid cooling systems designed in this way are also able to stop thermal runaway before it starts. By ensuring that a cell is operating in optimal conditions at all times, it also improves performance and lifespan, but even in the case of a damaged cell failing, the cooling system will be able to remove more energy than is produced, keeping adjacent cells cool. The battery avoids the chain reaction of thermal runaway and stays within operational parameters.
Some systems today are designed as add-ons that only cool the exterior of the cell or use air cooling technology – which requires 3,500 times more air flow volume to achieve the same heat removal, and require expensive add-on HVAC systems.
Despite the confidence that manufacturers can provide with holistically designed cooling systems, the risk of thermal runaway from incidents of catastrophic failure will always persist to some degree. Shipowners must also be confident that such a failure would not put their crew or vessel in danger.
This type of catastrophic failure is extremely rare in a liquid cooled system, but a last layer of safety can be delivered through direct venting mechanisms which, despite the clear need for this to work seamlessly with other safety mechanisms, are not often integrated with the ESS design. Such venting mechanisms remove flammable and toxic gasses from the battery, never allowing them to even enter the machinery room. Not only does a directly vented battery reduce explosion risk, it also allows emergency and service personnel to renter and secure the area far sooner than an unvented system. This venting system must be explosion-proof, and it must be entirely fool-proof – it must be designed to work regardless of how other parameters have been set by crew. This means it must be provided alongside specialised control units, and architecturally it must vent the gas to an appropriately safe environment.
Safer systems can cut costs
Safe design, as well as proper maintenance, means better performance – and a longer service life before replacement.
Using a fully optimised cooling system can aid efficiency to such a degree that an ESS can operate at an average continuous rate of 300%. This means that a 1MWh system can be met with a 333kWh battery; meaning a smaller, lighter, lower cost and easier to install system. It also means that systems degrade slower, and less redundancy must be built in.
Lower discharge rates mean a much bigger battery must be created to do the same duty, increasing costs and adding to the space and weight used.
Reducing the need for full system replacements is also important as many companies adopt rigorous sustainability standards.
One of the most important innovations in this space comes in the form of Sterling PBES’s CellSwap technology. As part of the battery architecture, CellSwap allows for individual battery cells to be easily removed and replaced without the replacement of an entire battery system. This simple maintenance can be performed at sea, reducing downtime. Because only the cells are replaced, the vessel owner only pays for the cells and the service to install them.
CellSwap also allows shipowners to benefit from consistent advances in battery cell technologies over time, as battery science constantly finds new ways of storing more power in smaller cells and improving cell safety and lifespan.
Demand for marine energy storage is already soaring. Countless vessels are already proving the cost benefits of electric of hybrid electric solutions, while future technologies and regulation – coupled with improvements in system technology – are expected to make it an even more attractive prospect for shipowners.
At this crucial time for the industry, suppliers must ensure that they build trust with shipowners and integrators by designing the safest, and most efficient, complete systems. In this way, the shipping industry will realise the full potential of energy storage and maximise their return on investment.