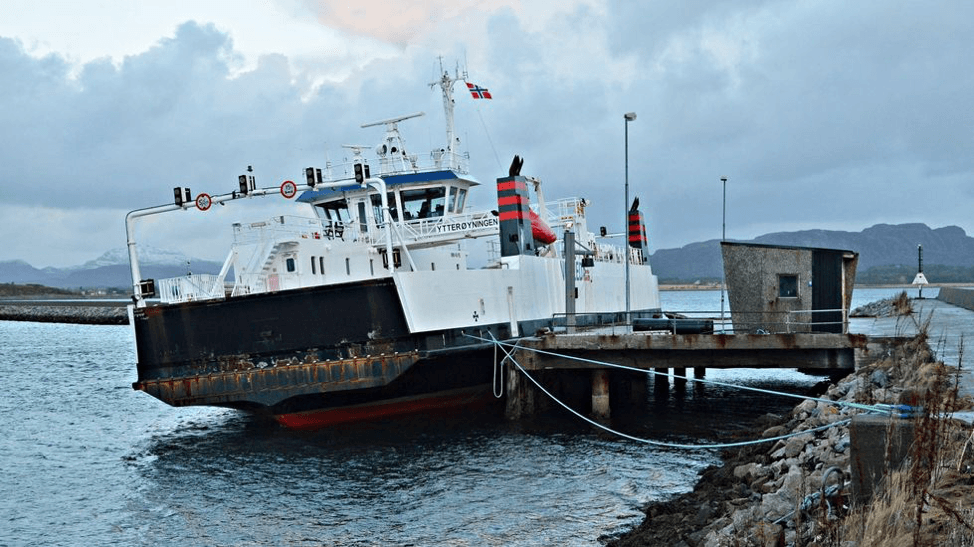
By Brent Perry and Grant Brown, Sterling PBES Energy Solutions (SPBES)
Preface
On October 11, 2019, an explosion rocked passenger ferry Ytterøyningen while dockside at Sydnes, Norway. The vessel, recently refit with a lithium-ion battery hybrid drive, is part of the new fleet of low and zero emission vessels being deployed across Norway and other parts of the world. The vessel was at dock having been pulled from service the night before due to a fire in the lithium propulsion batteries; a condition known as thermal runaway. The root cause of the fire is still to be announced, but the secondary explosion caused significant structural damage to the vessel; likely a result of a buildup of flammable gasses below deck. Thankfully none of the 15 people admitted to the hospital were badly injured and all were soon released.
The concern of all parties in this industry is the root cause of the fire, the explosion and the impact of this event on our industry currently. The impact to future vessels incorporating lithium storage systems also must not be ignored. Based on a lifetime of experience in the marine industry, the following are my personal opinions and observations about how we can reduce passenger risk and increase vessel safety and reliability.
History
When we founded this industry in 2009, the initial concerns that we had to address were centered initially around actual performance and safety. The questions were simple: Does large scale lithium energy storage actually have the capability to optimize or replace fuel driven engines? Can this be done with the same safety and reliability of current commercial marine systems? The next consideration was cost: Could lithium ESS actually match or improve the financial operating costs of commercial marine installations? And lastly, did lithium energy storage improve the environmental impact of the commercial marine industry.
At the time, lithium ESS was priced at around $3000/kWh, making it too expensive for widespread commercial adoption, and it was not available in a form factor that could support industrial scale marine installations. Simply put, the technology was not commercially viable. This lead me and my partners to take advantage of our unique position as marine people with strong battery knowledge to design the first “fit for purpose” lithium battery; one that was scalable to deliver MW scale power on a continuous basis. Our efforts, along with the support of the type approval agencies, flag authorities, fleet operators and system integrators (and a host of un-named people who all supported the dream of an emissions free marine industry), led to the acceptance of the use of lithium ESS in support of both hybrid electric installations and full electric vessels.
By 2014, the price of lithium ESS was approaching $1000/kWh and was regarded as a commercially acceptable solution in the marine industry, centered on Northern Europe and Scandinavia. Government legislation in this market area presented us with an opportunity to support environmental targets, while delivering better financial results than conventional technology. An added bonus was actually reducing risk and improving safety of vessels overall. There were still a lot of challenges. We were all learning as we went about how to engineer better and safer systems. At this point other companies saw a viable market and a chance for successful commercial use of their own lithium-ion solutions. The revolution was firmly rooted and taking hold of the industry. Most newbuilds were considering use of ESS in some form and many systems were being deployed.
Of course, the challenges started to grow as well. Now that we knew it worked, we had to figure out how to make it safer and more reliable while reducing cost. There are a lot of lithium solutions that are significantly cheaper than what meets the unique needs of the marine industry, but these are produced to serve markets with very different performance requirements than exist in commercial marine. The inflow of battery supply has created a growing demand on the type approval agencies and government authorities to further define the standards and safety criteria. The overwhelming number of technologies available present a dizzying variety of potential issues to anticipate and manage in defining the standards.
“In the rush to make this technology affordable, we cannot avoid the necessary steps to maintain safe operation. Safety is first and paramount always.”
Brent Perry, CEO, Sterling PBES Energy Solutions
Evolution
Experts estimate that all modern commercial vessels will soon have some form of energy storage on board. Each year there are more and more hybrid or fully electric ships navigating waters worldwide. These ships range in type from ferries transporting thousands of people daily, to offshore supply vessels and now even cruise ships. These vessels increasingly rely on lithium-ion energy storage as a power source, with modern designs containing hundreds of individual modules (batteries). The technology has proven itself reliable and powerful, but lack of performance history means lessons in safety are being acquired through daily operation. This is new technology and knowledge is being gained in real time. Safety systems need to be validated and must be kept as the highest priority.
As the industry founders that brought the first purpose designed energy storage to large marine projects, here is our opinion on what changes need to be made to improve safety.
The ferry Ytterøyningen at Brekstad. Photo: Alexander Killingberg
Testing & Certification
One of the biggest risks for batteries is not just fire, it is overall thermal management. Onboard the Ytterøyningen, the fire may have appeared to be under control, but the possibility for a lithium fire to continue to smolder is very real. As long as there is energy within the cells, risk remains of further fire and gas production. In our early days, our engineers were involved in automotive testing. In the course of these tests we observed one lithium fire that (in a controlled environment) took two full days to fully exhaust its energy and ultimately be extinguished. Aboard Ytterøyningen, I suspect that the batteries were damaged in some way and additional lithium-ion cells continued to fail after the initial fire occurred. The subsequent thermal runaway produced the gasses that ultimately led to the explosion the next day.
Thermal runaway occurs if the lithium-ion cells used in marine batteries are subjected to mechanical abuse, suffer from internal manufacturing defects, or operate over or under the correct voltage or internal temperature. In these situations, heat may be generated within the lithium-ion cells which may in turn increase to a point whereby it melts the separators inside the cells. This causes a reaction between the cathode material and electrolyte and can result in the temperature increasing until the cell vents toxic and flammable gasses. If ignition occurs, these gasses can create an unpredictable fire which can be very difficult to extinguish. In large enough concentrations in an unvented room, these gasses are also capable of creating very large explosions.
The minimum requirement for batteries used in commercial vessels in Norway is the Propagation Test Type 1. To receive certification this test is repeated three times and is intended to show prevention of propagation of the thermal event from one cell to the next. Simply put, this test means that if a cell in a single module ignites, fire may consume the single cell but will not enter thermal runaway and ignite the other cells in the module; thus the larger system remains safe.
Isolating a thermal event to one cell makes sense but reliance on this standard on its own creates potential problems:
1) The gasses that escape from even one cell are very flammable and are dangerous in an enclosed space. Proof of management of dangerous gases is required.
2) What occurs when more than one cell is involved right from the beginning of the event?
3) What happens when a module full of cells fails or even an entire system?
4) How can software help to predict and prevent a physical incident?
Testing to validate the design of batteries needs to expand to incorporate the risks we identify above. There is enough demonstrated market in the growing use of ESS to rationalize the furtherance of testing standards. It is a natural next step and will keep the focus on best engineering practices all around to minimize risk.
Testing – Next Generation
The technology exists today to nearly eliminate risk of battery failure, starting with fundamental safety systems that are not uniquely dependant on software. These hardware-based systems are complimented by software that can effectively alert the operator of real risk. Further, they must be incorporated with system testing to define the risks for whole system failures. This means that in testing a system, it has to be able to demonstrate gas extraction; that is removing risk of gas exposure to crew and firefighters and dispersing it so that the risk of explosion is mitigated. Safety testing must involve overcharging a pack so that cell failures are forced in more than one location, so that total safety management can be observed. It requires software that is able to continue to deliver important voltage and temperature related alarms at all times, not just when a system is in operation.
Combined with existing tests, this next generation of testing will be a very strong forward step to reducing the fears of operators. It will inspire reputable battery companies focussed on the needs of the industry to be better partners and prevent the others from bringing inappropriate solutions to market. This will reduce commercial risk instead of creating inevitable issues on board the very vessels that are at the core of this growing market.
The image is a screen capture of an SPBES baseline test to show the energy contained in a single cell. A typical commercial vessel may carry many thousands of these cells.
Image 2 Lithium Cell Fire.JPG – Link to https://youtu.be/kZsqzAx-Svs
The Solution – Prevent Thermal Runaway
Liquid cooling is the only safety system currently tested and proven to prevent thermal runaway. These active cooling systems prevent batteries from entering thermal runaway by simply extracting more heat than the cells can produce. Similar to an engine block of an automobile, a low pressure, high volume closed loop of chilled water is circulated through the battery. SPBES has developed a proprietary and patented cooling system that takes this idea one step further and circulates coolant through the very core of the battery, around each individual cell in the system. SPBES CellCoolTM is able to remove more thermal energy than the cells can produce when in an overcharge or damage scenario, effectively preventing the cells from achieving the temperature needed to go into thermal runaway.
Independently validated testing shows that the SPBES system is so effective that it works even if the coolant pump is disabled. This means that even in the event of catastrophic damage to the vessel’s electrical system, the system will still protect the batteries. Due to its patented design, CellCoolTM also eliminates hot spots on the cells and maintains optimal cell temperature – thus increasing cycle life and overall lifespan.
In comparison, forced air cooling only cools the external surfaces of the cells and is ineffective at eliminating hot spots in the cells. An air-cooled battery requires around 3500 times more air flow volume than water flow volume to achieve the same heat removal. To try to compensate, the battery room for an air-cooled system requires a robust HVAC system, an extra cost not typically included in the battery price by the battery vendor. A system using a chiller plate is only able to cool one single surface of the module and is therefore unable to fully prevent hot spots or remove all of the thermal energy contained in a lithium-ion battery.
Additional Safety Considerations – Thermal Barriers and Venting
Effective internal thermal barriers are an essential part of lithium battery safety systems. SPBES Thermal-StopTM is a metal barrier integral to the structure of the battery that works similar to a firewall. It prevents an overheated, overcharged or damaged cell from propagating to the adjacent cell. The event is therefore isolated to one cell and does not affect the others. Ignition does not jump to adjacent cells because of the metallic barrier between them. Because SPBES batteries have a solid metal internal assembly, they are in effect armored and resist mechanical damage from external forces. Even in the event of a totally spontaneous combustion, the cooling system is able to prevent propagation from cell to cell. In testing of spontaneous cell failure, cell temperature approached 500 degrees centigrade, but the adjacent cells never were hotter than about 80C. Upon disassembly, the adjacent cells showed no visible damage – they looked like new.
The image is a screen capture of an SPBES thermal runaway test. Even with the cooling system disabled no thermal runaway event occurs. The graph shows the voltage and temperature increasing to the point of cell failure, and the subsequent cooling. In an air cooled system this thermal event could continue for hours or days until all the energy is released.
Image 3 Thermal Runaway Test.JPG – link to https://youtu.be/e3ZOvwBUmx0
In the event that a cell is damaged or overheated within a module, dangerous gases are released. It is therefore important for every battery systems to be vented to protect the crew from exposure and protect the vessel from explosion. E-VentTM is another SPBES patented system to vent flammable gasses safely away from the battery area using a one-way valve that opens at low pressure. Gas is removed by an explosion proof fan that operates continuously or upon heat or gas detection. When gas flow stops the valve immediately closes, restricting flow of air or gasses back into the battery. This simple system reduces risk of crew exposure or a secondary explosion. It thus allows the crew to safely re-enter the vicinity of the battery system sooner to make repairs and restore power.
Using the SPBES CellCoolTM system, the cells simply do not combust. In fact, when modules used in standard overcharge testing were disassembled and inspected, the cells that had been overcharged looked virtually identical to untested, brand new units, save a small rupture on the top of the cell near the terminals. Despite the fact that virtually no gas has been detected during these tests (typically a 75Ah cell can produce 120l of gas, with liquid cooling we reduce this amount to around 800ml), we understand the potential risks. Every system we install has integrated CellCoolTM and E-VentTM systems installed.
Conclusions – Will it happen on your watch?
Given the rapid uptake of the use of large format lithium-ion batteries it is difficult for regulators to stay abreast of technology changes. I believe it is in the best interest of the maritime industry to do everything possible to ensure crew, vessel and environmental safety. As the thought leaders of energy storage in the maritime industry, SPBES has always been willing to licence its safety systems to other manufacturers in order to improve safety. We are willing to help any organization, be it regulatory or supplier.
About SPBES
Since developing our system, SPBES has installed 21 MWh of lithium storage on 17 vessels. SPBES energy storage is the only energy storage system proven to stop thermal runaway. It has been engineered with performance and safety as the two guiding principles that direct the design. The resulting liquid cooling system is the only one that makes the battery last longer, work harder and ultimately reduce risk.
Please contact info@spbes.com for more information.
For news about SPBES or to sign up for news updates, please visit SPBES.com.