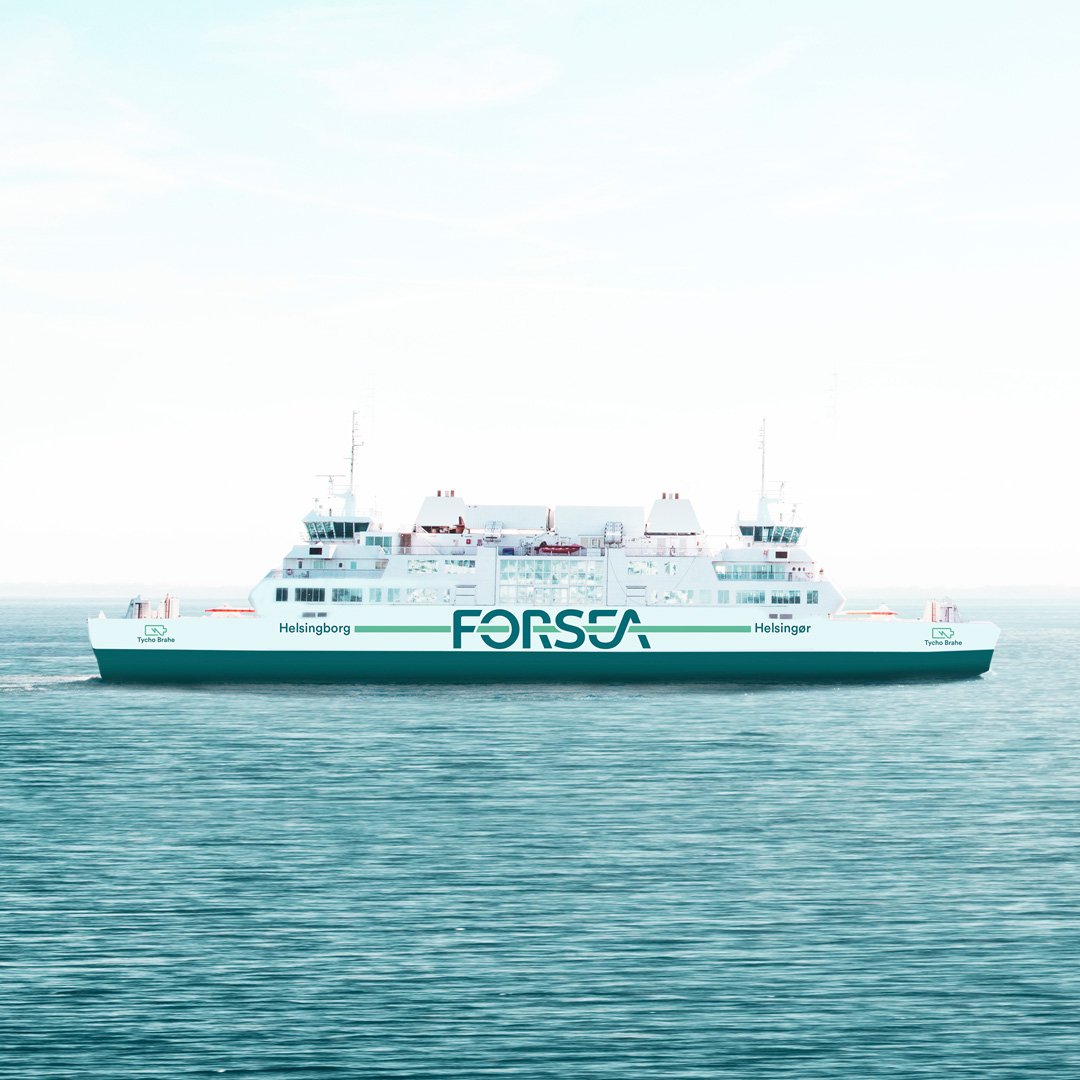
Published In Ship.Energy on October 1, 2020. Link to the article can be found here.
By Lesley Bankes-Hughes | Publishing Director, Petrospot Limited
‘In the future, every commercial vessel will have a battery room’’ says Sterling PBES CEO, Brent Perry.
In this Q&A with ship.energy, Brent Perry discusses the retrofit potential of Energy Storage Systems, lifecycle costs, payback times – and also explains how the technology is evolving to enable new applications – perhaps as a containerised solution or a microgrid, or for a new type of vessel
Is progress on the industry uptake of electric/hybrid vessels happening as Sterling PBES had envisaged? There seems to be an increasingly-held view that this technology is primarily appropriate for smaller vessels and/or those engaged on shorter, scheduled routes but that it will not have application for larger oceangoing vessels – do you agree with this viewpoint?
Over the past few years, smaller vessels and those engaged on shorter, scheduled routes have certainly been the primary beneficiaries of Energy Storage System (ESS) technology. Their size and capabilities have made electrification relatively simple, while owners have seen rapid return on investment (ROI) from electrification.
The operational benefits of energy storage have also traditionally been most pronounced in these markets. For passenger vessels, reduced vibrations and noise have clear benefits to passenger experience, while any near shore vessels are more exposed to national legislation and political or social pressure on greenhouse emissions and air pollution. This is changing as the industry comes under greater scrutiny from regulators and the public.
Where these segments are the greatest beneficiaries of ESS technology today, we are seeing larger vessels to take advantage of li-ion ESS systems in the coming years. New fuels with lower energy densities than traditional bunker fuels (ammonia, hydrogen, methanol) are expected to become commonplace over the next few years, and energy storage represents a particular efficiency benefit for these vessels in balancing the power output of any given fuel source.
What is the potential for the ESS retrofit market? Are there onboard installation challenges and also financial implications for this market versus newbuilds?
We believe that, where not all future vessels will be fully-electric, all future vessels will have a battery room and an ESS. For hybrid systems, an ESS’s infrastructure would not need to be changed if the other fuel used is at a later date. This means that an ESS can via retrofit, future proof a vessel now, cost effectively.
Historically, retrofit challenges have existed for ESS’s. Systems require some electrical infrastructure, and most systems require a specific footprint that can pose a challenge. New innovations are changing this, such as our new self-contained CanPower microgrid unit which can add energy storage to virtually any vessel. The system is simply, easily and inexpensively located on the top deck or other exterior location, and only requires a connection to the vessels electrical grid via a fixed connection or a plug in to function.
What are the vessel design challenges associated with the use of ESS?
It really depends on what you’re looking to do with an ESS. Adding a microgrid can be relatively simple, with a containerised system like our CanPower microgrid solutions being entirely self-contained and only requiring a minimal footprint and using existing infrastructure. With more challenging applications, existing type approval standards are there to apply to meet the expectations.
Holistic design of the entirety of an ESS and its surroundings is vital to ensure safety and operability. Minimising the footprint and size of a system can have a huge impact, and good design has huge benefits here. In the event of an accident, this holistic principle is even more important; designers need to be sure that toxic gasses would be vented into safe areas, and electronic control systems are fully integrated into a vessel’s other safety systems.
ESS manufacturers need to offer system integrators and naval architects expert support to overcome these challenges. At Sterling PBES, we take an active role in the design and installation of systems to provide seamless support to ensure efficiency, operability and safety.
Is there anything that the shipping sector can learn from the experiences of the automotive sector in relation to electric/hybrid technology?
If you look at the history of hybrid and electric cars, you can see how quickly electrification takes hold. At one point, electric and hybrid cars were seen as fringe and had little take up for decades, but when the technology caught up to the ambitions, we saw a sea change. Even Ferrari now make hybrid cars, and a lot of countries are planning to phase out conventional engine vehicles over the next two decades.
In the maritime industry, energy storage has been proven as a technology – especially for smaller vessels. We are currently seeing a similar change, as shipowners and other stakeholders take notice of the cost and emissions benefits of li-ion energy storage.
Could you comment on lifecycle costs/challenges of ESS in the context of a 25-30-year average lifespan of a vessel?
For most near shore vessels today, the fuel cost savings associated with energy storage represent a fast ROI that remains high throughout a vessel’s lifespan. However, this does not always tell the full story. A conventional ship engine would be expected to survive the normal lifespan of a ship without full replacement, while the useable lifespan of li-ion cells has historically meant full system re-builds are required every five to ten years.
Innovations like Sterling PBES’ CellSwap technology are changing this, though. CellSwap allows for individual li-ion cells to be replaced without removing the vital system infrastructure, meaning that a shipowner can take advantage of ever improving cell technologies without building in heavy redundancy into a system to improve its lifespan. At the same time, it makes replacing cells simpler than engine maintenance while bringing costs roughly in line with what you may see in a conventional vessel. Life cycle cost of electricity will be in the $0.05-0.06/kWh range.
Is standard contractual documentation in place for the operation of hybrid/electric vessels, i.e. charter party agreements?
Sterling PBES offers full financing options, either based on lease to own models or system cost sharing models where the customer pays for the system out of usage and service for the ESS. Today this is a viable option for all qualified clients and can involve total vessel finance or ESS system finance.
What is the payback period in terms of investing in hybrid vessels, and is financing available to owners for these vessels (subsidies, bank loans, other investment funds)?
Payback times really depend on a huge number of factors, including the size and purpose of a vessel, its average fuel costs, and where it is operating. We have seen some passenger vessels see a return on their investment within a year, while it is a longer-term investment for some other vessels.
Obviously, it is really important for companies to be open and honest in this space and we are committed to calculating these times honestly for our partners. As cell technology and energy density improves, it is important that the energy storage industry acts honestly and builds trust with the industry on payback times.
In terms of finance, we have seen end users engage with ESG investors and other green funds and initiatives. ESG is rapidly growing as an area for finance, and sustainable electrification fits perfectly with the ethos and mandate of this rapidly growing source of finance.
For fossil-fuelled vessels, there is a growing call for ‘well to wake’ emissions to be considered. How does this ‘measurement’ of emissions apply to ESS, in terms of production processes and also the disposal of lithium-ion batteries?
It is true that building and disposing of energy storage systems represents some environmental impact. Mining the materials needed, constructing and installing whole systems, and disposing of the heavy metals included in the cells can have emissions and ecological impacts. These are significantly fewer than with any other type of system.
At Sterling PBES, we are able to recycle and reuse 96% of the heavy metal content in the cells we use and use recycled material wherever possible. The materials are returned to ESS grade quality for true recycling.
At the same time, innovations like our CellSwap system mean that the infrastructure of an ESS does not need to be removed, disposed of, and replaced every time a system’s cells need replacing. This even further cuts the environmental impact of our systems, while also cutting costs, and is a philosophy the industry will need to implement as ‘well to wake’ issues are highlighted.
In your discussions with potential purchasers of electric vessels, what are the main questions they are asking of you in relation to the technology.
The market is very interested in where the historic limitations of ESS technology are changing, especially from the operational side. People want to know if you can use it in new, novel applications – perhaps as a containerised solution or a microgrid, or for a new type of vessel – in a cost efficient and safe way.
How do you see the electric/hybrid vessel sector developing over the next 10-20 years?
In the future, every commercial vessel will have a battery room. The technology has been proven from cost, operability and environmental perspective, while ESS technology will be a vital part of enabling new fuels as the industry prepares for a zero-carbon future.