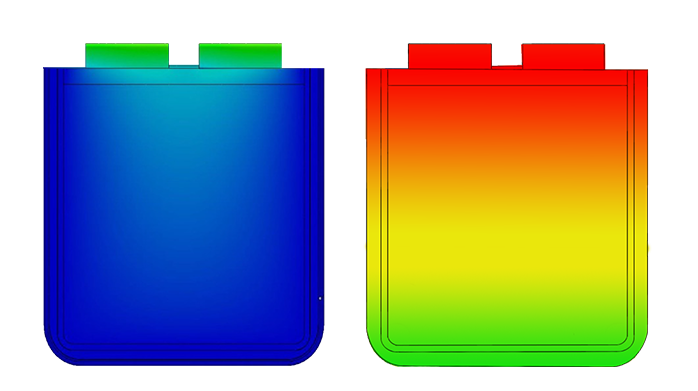
Each year there are more and more hybrid or fully electric ships navigating waters worldwide. All modern commercial vessels may soon have some form of energy storage on board.
These ships range in type from ferries transporting thousands of people daily to offshore supply vessels that maintain safety in critical oil rig operations. The ships increasingly rely on lithium-energy storage as their power source, with modern designs containing more than 1,000 individual modules (batteries). The technology has proven itself reliable and powerful, however, safety concerns linger and should be an utmost consideration for this new technology.

Not all battery systems are equipped with the same safety systems. Testing and certification for battery systems aboard ships has increased, but room remains to raise the bar higher.
One of the biggest risks for batteries is thermal runaway. Thermal runaway occurs if the lithium-ion cells used in marine batteries are subjected to mechanical abuse, suffer from internal manufacturing defects, or operate over or under the correct voltage or temperature. Heat is generated within the lithium-ion cells and causes a reaction between the cathode material and electrolyte. This can result in the cells’ temperature increasing until they vent toxic and flammable gases. If ignition occurs, these gases can be a fire hazard.
Currently, there are many battery solutions on the market that use an air-cooling system to try to maintain safe internal temperatures. The effective-ness is questionable, and the reliance on a thin-layer, fire-resistant separator between cells only reduces the fire risk from thermal runaway—it does not prevent it. It is far more sensible to take all reasonable precautions to eliminate thermal runaway from occurring in the first place.
Liquid cooling is the only safety system currently tested and proven to pre-vent thermal runaway. Liquid cooling prevents batteries from entering thermal runaway by simply extracting more heat than the cells can produce. Similar to an engine block of an automobile, a low-pressure, high-volume closed loop of chilled water is circulated through the battery. Taken a step further, coolant can be circulated through the alloy core of the battery, around each individual cell, enabling removal of more thermal energy than the cells can produce when in an overcharge or damage scenario.
In comparison, forced-air cooling only cools the external surfaces of the module and is ineffective at eliminating hot spots in the cells. An air-cooled battery requires around 3,500 times more air-flow volume than water-flow volume to achieve the same heat removal.
Read the full article here.