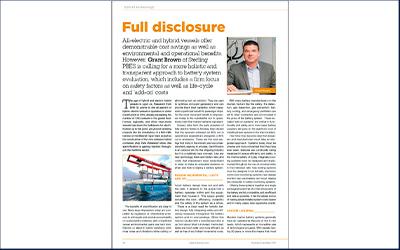
All-electric and hybrid vessels offer demonstrable cost savings as well as environmental and operational benefits. However, Grant Brown of Sterling PBES is calling for a more holistic and transparent approach to battery system evaluation, which includes a firm focus on safety factors as well as life-cycle and ‘add-on’ costs
Published in Bunkerspot by Grant Brown. https://www.bunkerspot.com/images/mags/flipbook/bs_v17n2_AprilMay20/mobile/index.html#p=67
The age of hybrid and electric hybrid vessels is upon us. Research from DNV GL points to 356 all-electric or hybrid-electric vessels in operation or under construction in 2019, already surpassing the number of LNG vessels in the global fleet. Ferries, tugboats, and other near-shore vessels have been the trailblazers for electrification up to this point, yet ground-breaking projects like the installation of a 600 kWh battery on the Maersk Cape Town as well as the construction of the zero emission hybrid container ship Yara Birkeland show that electrification is gaining traction through-out the maritime sector.
The benefits of electrification are clear to see. Many large shipowners today are compelled by regulatory or shareholder pres-sure to set targets and provide accountability on sustainability initiatives; with a traditional vessel environmental gains are hard won. Electric or electric hybrid solutions minimise noise and vibrations while cutting or eliminating toxic air pollution. They are used to optimise on-board generators and can provide black start capability, which represents a particular benefit to passenger ships. Yet the most important benefit to shipowners today is the substantial cut in operational costs that marine batteries represent. Indeed, data from the early adopters of fully-electric ferries in Norway have shown that the operator achieved an 80% cut in operational expenditure alongside a 95% cut in emissions. These are the cost savings that many in the industry are now understandably seeking to emulate. Electrification is an obvious win for the shipping industry but it is a relatively new concept. Like any new technology there are hidden risks and costs that shipowners must understand in order to make an educated decision on when and how to deploy a battery system.
HIDDEN INCREMENTAL COSTS ADD UP
Good battery design does not end with the cells. It extends to the space that a battery operates within and the equip-ment that houses it. This space greatly dictates the cost, efficiency, durability and the safety of the system as a whole. There is a clear need for holistic bat-tery design; fully integrating safety and effi-ciency measures throughout the battery system and its surroundings. When this need is coupled with a manufacturer who is up front about what is included, marine bat-teries are much safer and more efficient, as well as free of any hidden incremental costs.
With many battery manufacturers on the market, factors like fire safety, fire detection, gas detection, gas extraction, battery cooling, and emergency ventilation are left to other contractors and not included in the price of the battery system. These so-called ‘add-on systems’ are critical to functionality and safety, yet in most cases battery suppliers will pass on the significant cost of installing these systems to the ship’s builders. Over time it has become clear that designers and manufacturers must take an integrated approach. Systems today must be smarter and more connected than they have ever been, features are continually being developed to ensure efficiency and safety. In the marine battery of today, integrated cool-ing systems must be designed and implemented throughout the core of a module down to the individual cells. Gas venting systems must be designed to be fail-safe, electronic control and monitoring systems must always monitor key parameters and must always be connected to safety monitoring systems. Offering these systems together as a single package ensures that all of the critical parts of the battery are fully compatible, and as efficient and safe as possible. It has the added bonus of making actual installed system costs clearer and in many cases, less expensive overall.
YSTEM LIFESPAN
Modern marine battery systems generally have an operational lifecycle of five to ten years, which represents an incredible rate of technological progress. With vessels last-ing 30 years or more this means that most shipowners will have to deal with natural degradation and ultimately battery system rebuilds. Similar to a conventional ship’s engine hardware requiring a re-build sev-eral times in its lifespan, battery replacement represents an additional challenge. One of the most important innovations in this space comes in the form of SPBES’ CellSwap technology, which allows for individual battery cells to be easily removed and replaced without the replacement of an entire battery system. This significantly reduces replacement costs. Due to lower operational hours and reduced low load run time, CellSwap aligns more closely with the normal maintenance intervals of a traditional vessel’s propulsion gear. With regular CellSwap replacement intervals, shipowners can benefit from newer battery cell technology such as improved energy density, improved discharge rates and improved lifespan. This means that more usable power can be stored in the same sized batteries. The usefulness of this additional power depends on the amount of energy that is available on a continuous basis. As in any electrical component, heat is the enemy and efficient cooling increases both the system’s continuous rating and its lifespan. Robust cooling aids efficiency to such a degree that a system with fully integrated liquid cooling can operate at an average continuous rate of 300%. This means that a system requiring 1 MW at peak could easily be met with a 350 kWh battery; a much smaller, much lighter, and far less costly system to install and maintain. Many cooling systems on the market today do not evenly regulate the temperature of the core of the battery cells, which cuts lifespan and continuous rating. For a cooling system to be truly effective, it must cool the entire battery unit evenly. Most ‘add on’ systems, as well as air cooled systems, are not able to cool the entire battery completely. However, a fully integrated liquid cooling system can pro-vide the required thermal exchange by circulating chilled water through the very core of a battery, in effect similar to the cooling system on a traditional internal combustion engine. Fully integrated liquid cooling has the added benefit of being far more efficient than the air cooled counterpart and requires 3,500 times less water flow volume compared to air to achieve the same heat removal, removing the need for expensive add-on HVAC systems.
SAFETY AS PRIORITY
While the industry sits up and takes notice of the cost savings and operational advantages that electrification offers, there is still consider-able and justifiable concern about safety. The most prominent safety issue associated with lithium ion marine batteries is thermal runaway. Thermal runaway occurs when a dam-aged or faulty cell overheats, damaging the cells that surround it and emitting highly flammable and toxic gasses that may ignite. The adjacent cells damaged by the initial faulty cell also overheat, thus creating a thermal chain reaction that will continue until all the energy in the battery is depleted. As we gain more practical experience, these risks must be dealt with honestly and mitigated. A holistic battery design is key, with all parts of the system designed to work together with safety at its core.
This starts with the cooling system. An effective liquid cooling system integrated into the core of the cells is the first line of defence against thermal runaway. Effective liquid cooling can cool a battery faster than it can heat up in a thermal runaway incident. This stops the chain reaction before it starts. Yet the risk of thermal runaway cannot be removed entirely, so failsafe mechanisms beyond cooling further reduce the risk to the crew and vessel. Venting mechanisms can remove flammable gasses from an unstable battery, reducing the risk of explosion as well as the risk posed by toxic fumes. Thermal barriers between cells can also help to reduce the risk of a damaged cell from starting a thermal chain reaction. These are exciting times for marine battery systems. Demand and viability are growing at an amazing pace, as is supporting infrastructure. As manufacturers, we must ensure that we bring the best possible batteries to market. We must do this as cost efficiently as possible, with safety always being the number one priority. To do anything else makes marine batteries needlessly expensive to install or creates needless risks to shipowners. This holistic, safety first approach will require that battery manufacturers develop and offer fully formed systems that provide the highest in safety, value, and ultimately, return on investment.